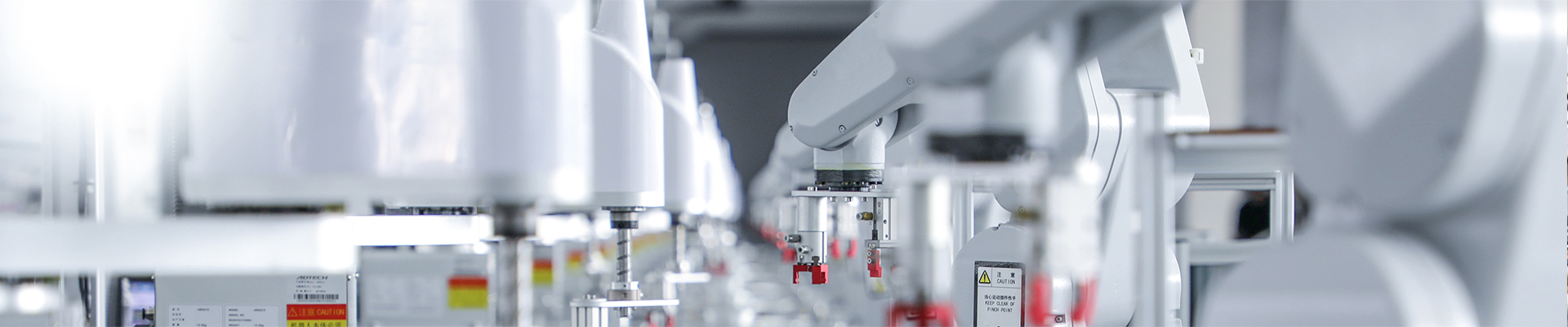
How to choose the right torque for a torque-limiting magnetic coupling
2025-04-07 08:04Magnetic couplings (MCUs), comprising a copper rotor, a permanent magnet rotor, and a controller, revolutionize power transmission by enabling a "soft" magnetic connection between motors and driven machinery. Unlike traditional mechanical couplings, they eliminate physical contact, reducing wear and enabling precise torque control through air-gap adjustments. This technology is widely adopted in industries requiring overload protection, vibration damping, or precise speed regulation, such as chemical processing, HVAC systems, and renewable energy applications. This guide expands on torque selection principles, technical nuances, and practical considerations to help engineers optimize performance.
1. Magnetic couplings working Principles and Torque Transmission Mechanisms
Magnetic couplings operate on the principle of eddy current induction. When the motor-driven copper rotor rotates, its magnetic field induces eddy currents in the adjacent permanent magnet rotor, creating torque without mechanical linkage. The air gap between rotors acts as a critical control parameter:
Smaller Air Gap: Enhances magnetic flux density, increasing torque transmission efficiency .
Larger Air Gap: Reduces torque but allows slip for overload protection, a defining feature of torque limited magnetic couplings.
This non-contact design minimizes maintenance and eliminates lubrication needs, making MCUs ideal for harsh environments (e.g., corrosive or explosive atmospheres) .
2. Torque Characteristics by Magnetic Coupling Type
2.1 Fixed Magnetic Couplings
Torque Range: Typically 10–20 N·m .
Design: Utilize permanent magnets for static torque transmission.
Applications: Precision instruments, small pumps, and high-speed/low-load scenarios where consistent torque is critical.
2.2 Torque Limited Magnetic Couplings
Functionality: Integrate slip mechanisms to cap maximum torque, preventing system overloads. For example, in conveyor systems, they protect motors during sudden jams.
Adjustability: Torque limits can be preset or dynamically adjusted via controllers.
Industries: Mining, manufacturing, and material handling.
2.3 Electromagnetic Couplings
Torque Capacity: Up to 500 N·m or higher, depending on electromagnetic coil strength.
Control Flexibility: Real-time torque adjustments via variable currents, suitable for heavy machinery like crushers or wind turbines.
Efficiency Trade-offs: Higher energy consumption compared to permanent magnet types.
3. Key Factors Influencing Torque Performance
3.1 Speed-Torque Relationship
Torque transmission efficiency decreases at higher speeds due to eddy current losses and heat generation. For instance, an MCU rated for 50 N·m at 1,500 RPM may deliver only 40 N·m at 3,000 RPM.
3.2 Temperature Effects
Permanent Magnets: High temperatures (above 80°C) can demagnetize neodymium-based magnets, reducing torque by up to 15% .
Copper Rotor: Thermal expansion alters air gap dimensions, necessitating thermal compensation in precision applications.
3.3 Medium Viscosity
In fluid-driven systems (e.g., pumps), viscous media increase drag forces, requiring higher torque margins. For example, pumping crude oil vs. water may demand a 20% torque buffer.
4. Selection Guide
When selecting a magnetic coupling, prioritize:
Torque requirements: Meet the load demands of the application.
Efficiency and durability: Ensure long-term reliability under operating conditions.
Cost-effectiveness: Balance initial investment with maintenance requirements.
Conclusion
Understanding torque characteristics and factors that influence them is critical to optimizing magnetic coupling performance. Whether you choose a fixed, torque-limited, or electromagnetic type, combining specifications with application needs ensures efficient and reliable power transmission.