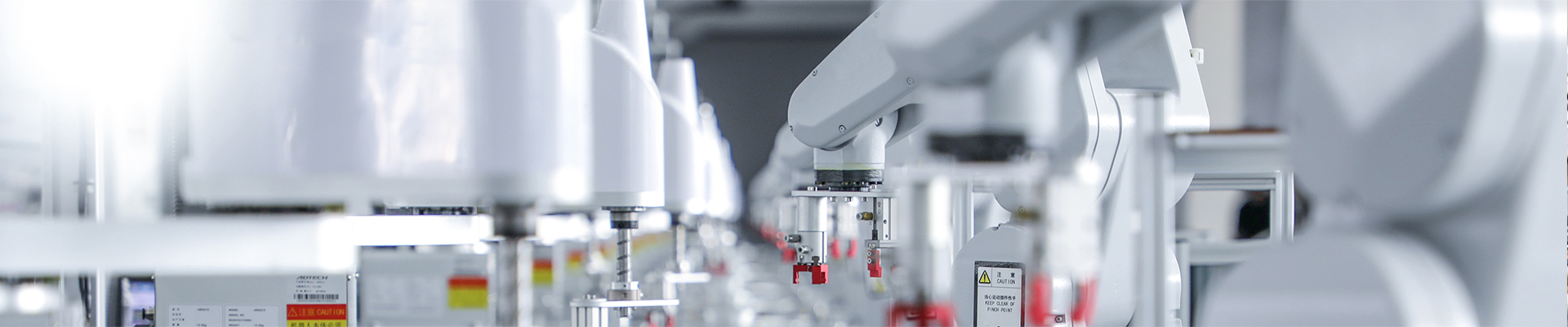
Hydraulic clutch of the slow-fill chamber with liquid: Working principle, advantages and application
2025-04-21 09:35A fluid coupling with a delay chamber is a specialized type of hydrodynamic coupling that provides exceptionally smooth starting of mechanisms with high inertia and effective protection of the drive from overloads. The key feature is the presence of an additional chamber (delay chamber), temporarily holding part of the working fluid during start-up. This allows the engine to quickly pick up speed with almost no load, after which the fluid gradually flows into the working chamber, smoothly increasing the transmitted torque. This mechanism makes it an ideal solution for belt conveyors, crushers, mills and other machines with difficult starting conditions.
What is a fluid coupling with a delay chamber?
A standard fluid coupling transmits rotation from the drive shaft (engine) to the driven shaft (working machine) via the working fluid, providing smoothness and protection from overloads without a rigid mechanical connection. A fluid coupling with a delay chamber improves on this concept by adding one or more delay chambers. These chambers communicate with the main working area of the coupling through calibrated holes (nozzles), the size of which can sometimes be adjusted to set the starting time.
The operating principle of a coupling with a delay chamber
The operating principle of a fluid coupling with a delay chamber is to temporarily reduce the volume of the working fluid in the main chamber during engine acceleration:
Idle: Part of the fluid is in the delay chamber(s).
Startup: The engine rotates the pump wheel. Due to the small amount of fluid in the working area, the transmitted torque is minimal (120-150% of the nominal, depending on the design). The engine quickly accelerates with a low starting current.
Machine acceleration: Under the action of centrifugal force, the fluid from the delay chamber gradually flows through the nozzles into the main working chamber. The transmitted torque smoothly increases, accelerating the working machine.
Working mode: All the fluid is in the working chamber, the coupling transmits torque with minimal slip (usually 1.5-6%).
Designs with an enlarged or double delay chamber (e.g. TVV, CCK types) provide even longer and smoother starts, which is important for applications such as long fluid couplings for conveyors.
Key benefits of use
The use of a fluid delay chamber coupling provides significant benefits:
Exceptionally smooth start: Reducing the starting torque to 120-150% of the nominal minimizes shock loads, extending the service life of all equipment (belts, gearboxes, chains).
Motor protection: "No-load" start-up reduces starting currents, prevents overheating, allows the use of standard asynchronous motors and simplifies the control system.
Reliable overload protection: The fluid coupling automatically limits the maximum transmitted torque, preventing damage to the motor and machine in the event of jamming or a sharp increase in load.
Vibration damping: The hydraulic connection effectively absorbs torsional vibrations and shocks.
Energy saving: Reducing peak starting currents reduces overall energy consumption.
Load balancing: In multi-motor drives, fluid couplings help to distribute the load evenly.
Durability and low operating costs: The absence of wearing friction elements in the transmission of the main torque ensures a long service life and minimal maintenance of the fluid coupling.
Main areas of application
The use of slow-filling fluid couplings is most appropriate in high-power drives with large inertial masses:
Belt and scraper conveyors (especially long and loaded).
Heavy crushers (jaw, cone, hammer) and mills (ball, rod).
Powerful pumps and fans.
Centrifuges, separators, decanters.
Drives of rotary excavators, lifting mechanisms.
Other machines requiring controlled, smooth start-up by a fluid coupling.
How to choose a fluid coupling with a delay chamber
The correct choice of a fluid coupling with a delay chamber requires an analysis of the following parameters:
Engine power and speed: Determine the main size of the coupling.
Load characteristics: Moment of inertia of the driven machine (WR²), required starting torque, operating mode (stable, intermittent, reversible), starting frequency.
Required acceleration time: Affects the choice of the delay chamber type (standard, extended, double) and settings (if applicable).
Operating conditions: Ambient temperature, presence of dust, moisture, explosive atmosphere (ATEX version required).
Mounting design: Type of shaft connection (direct, via an elastic element, with a belt pulley, with a brake disc/drum).