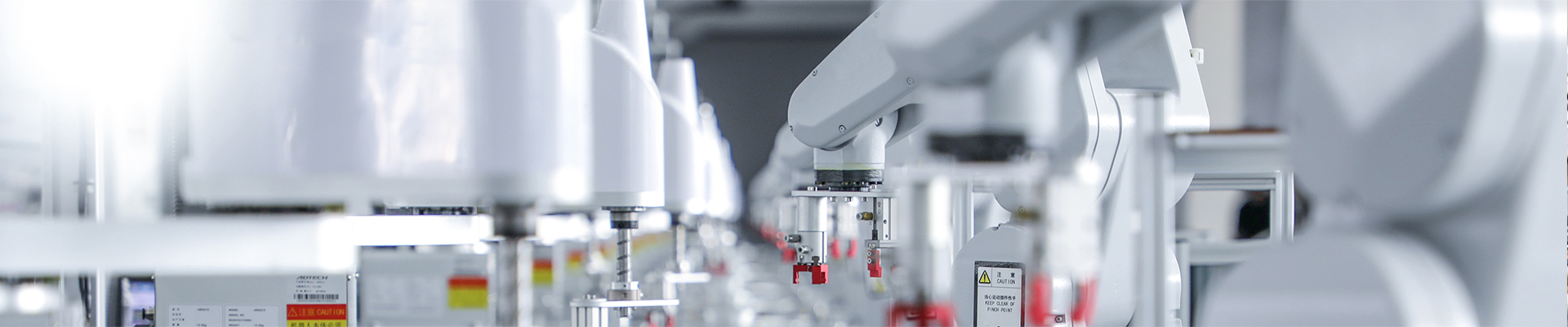
Decoding the Working Principle of Magnetic Coupling
2025-04-24 16:30News Release: Decoding the Working Principle of Magnetic Coupling – The Core Technology Revolutionizing Industrial Power Transmission
April 24, 2025
Magnetic Coupling, as an innovative technology in modern industrial power transmission, has gained widespread adoption in industries such as chemical processing, pharmaceuticals, and energy due to its non-contact operation and high efficiency. Its core working principle, based on magnetic field coupling effects, breaks through the physical limitations of traditional mechanical transmission systems, offering groundbreaking solutions for enhanced equipment safety and energy efficiency.
I. Core Mechanisms of Operation
Magnetic Field-Driven Non-Contact Transmission
A Magnetic Coupling consists of two key compositions it as a cornerstone of sustainable and intelligent manufacturing. As material science and automation advance, Magnetic Couplings are poised to unlock new frontiers in green energy and precision engineering.ponents: the drive rotor (active end) and the driven rotor (passive end), which are physically separated by an air gap and lack mechanical connections. When the drive rotor is rotated by a motor, its permanent magnets or electromagnets generate a rotating magnetic field. This field penetrates the air gap and interacts with the conductive material (e.g., copper rotor) on the driven rotor, inducing eddy currents within it. These eddy currents produce a counteracting magnetic field, creating torque that synchronizes the rotation of the driven rotor with the drive rotor.
Dynamic Adjustment and Precision Control
The transmitted torque and rotational speed can be flexibly regulated by adjusting the air gap distance or magnetic field intensity. For instance, speed-adjustable Magnetic Couplings achieve precise load-side speed control by modulating the air gap, reducing inrush currents and mechanical shocks during startup.
II. Technical Advantages and Application Scenarios
Zero Wear and Extended Lifespan: Non-contact transmission eliminates friction between mechanical components, significantly prolonging service life.
Leakage Prevention and Enhanced Safety: A sealed isolation sleeve design ensures complete containment, making it ideal for hazardous environments involving flammable, explosive, or corrosive substances.
Energy Efficiency: Compared to traditional hydraulic couplings, Magnetic Couplings reduce energy losses by over 20% due to higher transmission efficiency.
Key Applications:
Chemical and Pharmaceutical Industries: Used in agitators and pumps to prevent leakage in reactors handling toxic fluids.
Energy Sector: Deployed in cooling systems for power plants to enhance reliability and reduce maintenance costs.
Water Treatment: Applied in pumps and compressors for corrosion-resistant and vibration-damped operations.
III. Structural Variations and Innovations
Radial vs. Planar Magnetic Couplings
Radial Magnetic Couplings: Utilize inner and outer magnetic rings with tangential magnetization, enabling torque transmission through radial magnetic fields. The isolation sleeve, often made of non-magnetic stainless steel, ensures leak-free performance in high-pressure systems.
Planar Magnetic Couplings: Optimize magnetic pole arrangements on parallel discs, improving torque density and alignment flexibility for compact machinery.
MagnaDrive Technology
A breakthrough design by MagnaDrive (USA) employs rare-earth neodymium magnets and copper rotors. By adjusting the air gap between the conductor and permanent magnet rotors, it achieves 98.5% transmission efficiency while enabling soft starts and overload protection.
Intelligent Control Systems
Advanced models integrate controllers to automate air gap adjustments based on real-time load demands, further optimizing energy consumption in HVAC and industrial cooling systems.
IV. Case Study: Magnetic Couplings in Coking Plants
In coking facilities, Magnetic Couplings have replaced traditional shaft seals in centrifugal pumps handling high-temperature tar. By eliminating mechanical wear and leakage, they reduce downtime by 40% and cut annual maintenance costs by approximately $120,000 per unit. The technology also supports variable frequency drives (VFDs) to adapt to fluctuating production demands, showcasing its versatility in heavy industries.
V. Future Trends and Developments
High-Temperature Superconductors: Research into superconducting materials aims to minimize eddy current losses, enabling Magnetic Couplings to handle megawatt-scale power transmission in wind turbines and marine propulsion systems.
Smart Manufacturing Integration: IoT-enabled couplings with embedded sensors will provide real-time diagnostics for predictive maintenance, reducing unplanned outages.
Hybrid Designs: Combining electromagnetic and permanent magnet systems will allow dynamic torque adjustments without physical air gap changes, expanding applications in robotics and aerospace.
Conclusion
Magnetic Coupling technology, leveraging the invisible force of magnetism, has redefined power transmission paradigms in industrial settings. Its non-contact operation, coupled with unparalleled reliability and efficiency,