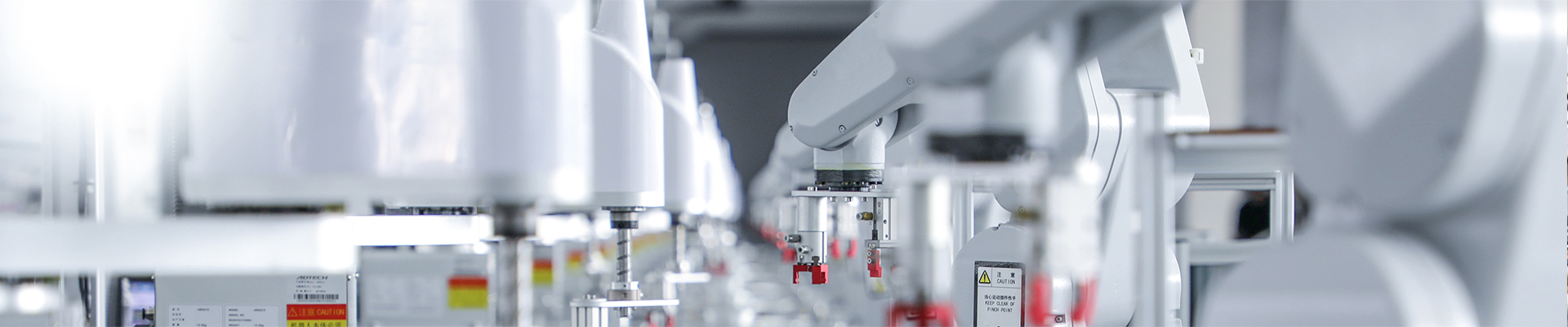
Principles of Ribbed Coupling
2025-04-11 08:38Principles of Ribbed Coupling
I. Definition and Basic Characteristics
A ribbed coupling is a torsionally rigid mechanical transmission component characterized by zero-backlash torque transmission. It maintains rigid connectivity even under load-induced shaft misalignment, making it suitable for low-speed, high-torque applications requiring precise shaft alignment.
II. Working Principles
Torque Transmission Mechanism
Power is directly transferred between driving and driven shafts via rigid connections (e.g., bolts, tenons, or sleeves). For ribbed couplings with reamed-hole bolts, torque relies on shear and compression forces from bolt shanks, while standard bolt versions utilize end-face friction.
Alignment Methods
Protrusion-groove engagement: Achieves self-alignment through precision-machined convex-concave structures
Split-ring assembly: Employs segmented rings for positioning
Reamed-hole bolts: Enforces alignment via high-precision bolt holes
III. Ribbed coupling structural Variants
Flange Coupling: Features flanged half-couplings connected by high-strength bolts, available in standard or reamed-hole bolt configurations. Ideal for heavy-duty, low-speed systems (<30 m/s).
Sleeve Coupling: Uses a one-piece sleeve with keys/pins for torque transfer, suited for compact low-power machinery.
Split-Shell Coupling: Modular shell design for easy installation, commonly used in marine propulsion systems.
Parallel-Shaft Coupling: Adopts gear/chain mechanisms for parallel shaft compensation.
IV. Performance Features
Advantages:
Transmission efficiency exceeds 98% with no elastic hysteresis loss
Simple structure and low maintenance costs
Resistant to oil, corrosion, and harsh environments
Limitations:
Requires shaft alignment accuracy ≤0.05 mm
Lacks vibration damping, unsuitable for shock loads
Maximum speed limited by thermal expansion compensation
V. Technological Innovations
Advanced fully compensated ribbed couplings integrate multi-DOF compensation mechanisms, reducing alignment precision requirements by 50% while maintaining ±2% speed fluctuation tolerance. These enhanced designs show promise in CNC machine tools and marine propulsion systems.
VI.Ribbed coupling product application occasions:
1. Transmission devices:sleeve coupling are commonly used in various mechanical transmission devices, such as machinery, water pumps, fans and compressors.
2. Industrial equipment and machinery: In various types of industrial equipment,ribbed coupling are widely used to meet the needs of mechanical connection, rotation transmission and torque transmission.
3. Agriculture and agricultural machinery and equipment: Agricultural machinery and equipment in the agricultural industry, such as tractors, harvesters and planters, usually require ribbed coupling to connect driving components, transmission shafts and various working mechanisms.
4. Papermaking machinery: sleeve coupling play a key role in papermaking machinery and are used to connect various rollers, conveyor belts and cutting devices to ensure precise rotation transmission and coordinated work.
5. Conveying equipment: Whether it is a heavy-duty conveyor belt system or a light-duty conveying mechanism, sleeve coupling play an important role in these equipments and are used to connect transmission components such as motors and transmission wheels.