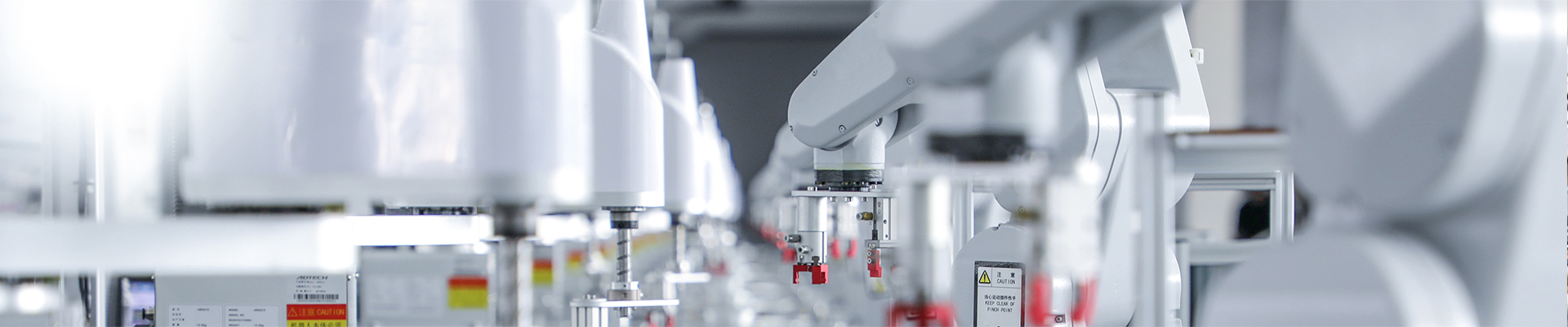
- Home
- >
- News
- >
- Coupling Basics
- >
Coupling Basics
2025-04-14 10:40A coupling is a device that connects two shafts or a shaft and a rotating part, rotates together during the transmission of motion and power, and does not disengage under normal circumstances. Sometimes it is also used as a safety device to prevent the connected parts from being subjected to excessive loads, and plays the role of overload protection.
Brief description of coupling
Coupling is also called coupling. It is a mechanical component used to firmly connect the driving shaft and the driven shaft in different mechanisms to rotate together and transmit motion and torque. Sometimes it is also used to connect shafts with other parts (such as gears, pulleys, etc.). It is often composed of two halves, connected by keys or tight fits, fastened to the two ends of the shaft, and then connected in some way. The coupling can also compensate for the offset (including axial offset, radial offset, angular offset or combined offset) between the two shafts due to inaccurate manufacturing and installation, deformation during operation or thermal expansion, etc.; as well as mitigate impact and absorb vibration.
Most commonly used couplings have been standardized or normalized. In general, you only need to correctly select the type of coupling and determine the model and size of the coupling. If necessary, the load capacity of the vulnerable weak links can be checked and calculated; when the speed is high, the centrifugal force of the outer edge and the deformation of the elastic element need to be verified, and the balance check needs to be performed.
Coupling type
Couplings can be divided into two categories: rigid couplings and flexible couplings.
Rigid couplings do not have the ability to buffer and compensate for the relative displacement of the two axes, and require the two axes to be strictly aligned. However, this type of coupling has a simple structure, low manufacturing cost, easy assembly and maintenance, can ensure that the two axes have a high degree of alignment, and transmit a large torque, and is widely used. Commonly used ones include flange couplings, sleeve couplings, and clamp couplings.
Flexible couplings can be divided into flexible couplings without elastic elements and flexible couplings with elastic elements. The former only has the ability to compensate for the relative displacement of the two axes, but cannot buffer and reduce vibration. Common ones include slider couplings, gear couplings, universal couplings and chain couplings. The latter contains elastic elements. In addition to the ability to compensate for the relative displacement of the two axes, it also has buffering and vibration reduction effects. However, the transmitted torque is generally not as good as that of flexible couplings without elastic elements due to the limitation of the strength of the elastic elements. Common ones include elastic sleeve pin couplings, elastic pin couplings, plum blossom couplings, tire couplings, serpentine spring couplings and leaf couplings.
Coupling performance requirements
Depending on different working conditions, the coupling must have the following performance:
(1) Movability. The mobility of the coupling refers to the ability to compensate for the relative displacement of the two rotating components. Factors such as manufacturing and installation errors between the connected components, temperature changes during operation and load deformation all put forward requirements for mobility. Movable performance compensates or alleviates the additional loads between shafts, bearings, couplings and other parts caused by the relative displacement between rotating components.
(2) Buffering. For occasions where loads are frequently started or working loads change, the coupling must have elastic elements that play a buffering and vibration reduction role to protect the prime mover and working machine from damage or no damage.
(3) Safe and reliable, with sufficient strength and service life.
(4) Simple structure, easy installation and maintenance.
Selection of coupling type
When selecting a coupling type, the following items should be considered.
① The size and nature of the required torque, the requirements for buffering and vibration reduction functions, and whether resonance may occur.
② The relative displacement of the two shaft axes caused by manufacturing and assembly errors, shaft load and thermal expansion deformation, and relative movement between components.
③ The allowable external dimensions and installation methods, in order to facilitate the operating space required for assembly, adjustment and maintenance. For large couplings, it should be possible to disassemble and assemble without the shaft moving axially.
In addition, the working environment, service life, lubrication, sealing and economy should also be considered, and then refer to the characteristics of various couplings to select a suitable coupling type.