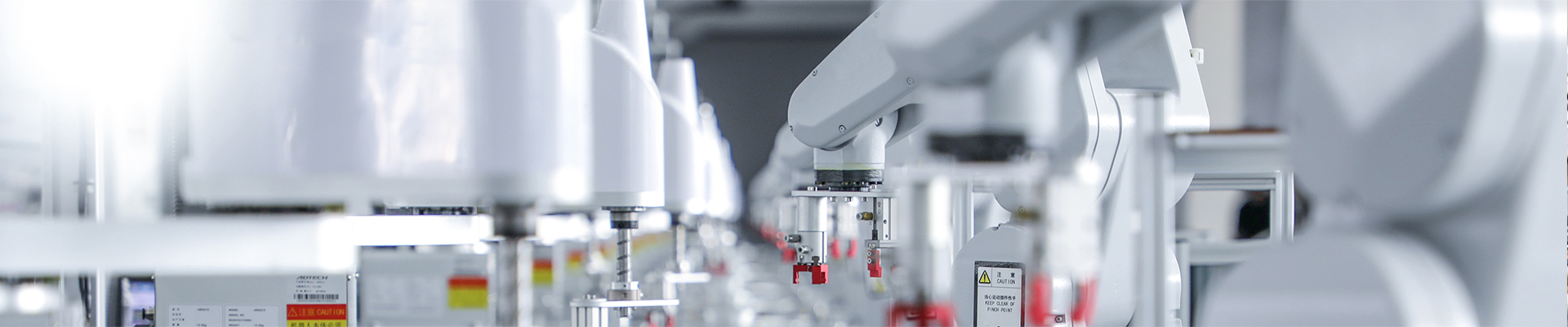
Introduction to Magnetic Coupling Technology
2025-03-11 08:57Speed Regulating Controller Magnetic Coupling: A Comprehensive Guide to Working Principles
Introduction to Magnetic Coupling Technology
Magnetic coupling, a revolutionary power transmission solution, enables contactless torque transfer through electromagnetic fields or permanent magnets. As an industrial game-changer, its integration with speed regulating controllers has redefined precision control in pumps, compressors, and HVAC systems. This article dissects the working principles of magnetic coupling with speed regulating controllers, combining electromagnetic theory with engineering applications.
Core Components of Magnetic Coupling Systems
1. Rotor Assembly
Drive Rotor: Connected to the motor shaft, embedded with permanent magnets (e.g., NdFeB) or electromagnetic coils .
Driven Rotor: Attached to the load, constructed from conductive materials like copper/aluminum alloys to induce eddy currents .
Isolation Barrier: A hermetic shield (typically 0.5–3 mm thick) preventing mechanical contact while allowing magnetic flux penetration .
2. Speed Regulating Controller
This electronic module adjusts output torque and RPM by manipulating:
Magnetic field strength via current regulation
Air gap distance between rotors
Phase alignment of electromagnetic poles
Working Principle: A Three-Stage Process
Stage 1: Magnetic Field Generation
When powered, the speed regulating controller energizes the drive rotor’s electromagnetic coils (or aligns permanent magnets), creating a rotating magnetic field. The field intensity follows:
Where:
( B ) = Magnetic flux density
( \mu_0 ) = Vacuum permeability
( \mu_r ) = Relative permeability of core material
( N ) = Coil turns
( I ) = Current from controller
( l ) = Magnetic path length
Stage 2: Eddy Current Induction
The rotating field induces eddy currents (( I_{eddy} )) in the driven rotor, governed by Faraday’s Law:
These currents generate a secondary magnetic field opposing the drive rotor’s motion, creating torque transmission.
Stage 3: Torque Regulation
The speed regulating controller magnetic coupling modulates performance through:
Speed Control Mechanisms
1. Slip-Based Regulation
The magnetic coupling speed controller intentionally creates slip (5–15%) between rotors. Slip power dissipation (( P_{slip} )) is calculated as:
Where ( \omega_{slip} ) = angular velocity difference.
2. Adaptive Field Weakening
For high-speed applications (>3000 RPM), the controller reduces field current to limit back-EMF, enabling extended speed ranges without mechanical wear.
3. Predictive Load Compensation
Advanced controllers use AI algorithms to anticipate load changes, adjusting magnetic parameters in <10 ms for seamless operation.
Advantages Over Traditional Couplings
Zero Mechanical Wear: Eliminates gear/bearing maintenance
Explosion-Proof Design: Ideal for hazardous environments (O&G, chemical plants)
Energy Efficiency: 92–97% efficiency vs. 80–85% in hydraulic systems
Precision Control: ±0.5% speed stability with speed regulating controllers.
Industrial Applications
Case Study 1: Petrochemical Pumps
High-pressure magnetic pumps (耐压 25 MPa) use magnetic coupling with speed control to handle volatile fluids. The isolation barrier prevents leakage, while adaptive torque matching reduces cavitation risks.
Case Study 2: HVAC Systems
Variable-speed magnetic couplings in chillers achieve 30% energy savings through dynamic load matching, regulated by PID-based controllers.
Future Trends in Magnetic Coupling Technology
High-Temperature Superconductors: Enabling 2× torque density improvements.
Integrated IoT Controllers: Real-time predictive maintenance analytics.
Multi-Physics Optimization: Combined electromagnetic-thermal-structural simulations.