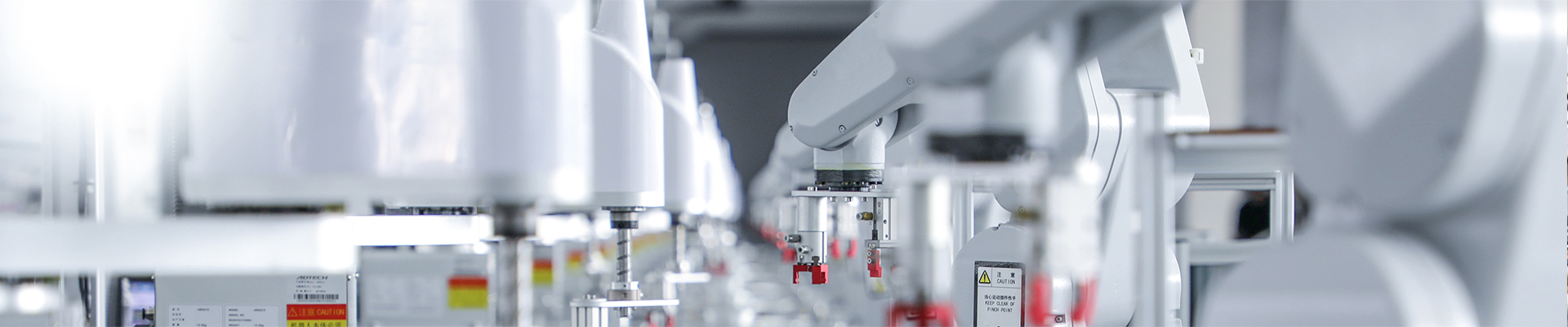
Working Principle of Fluid Coupling
2025-03-26 08:54Working Principle of Fluid Coupling
A fluid coupling is a non-rigid coupling that uses liquid as the working medium, primarily designed for transmitting and regulating mechanical energy. Its operation relies on kinetic energy transfer and momentum variation of the fluid.
Detailed breakdown of fluid coupling core working principles:
Basic Structure and Components
A fluid coupling mainly consists of a pump wheel, turbine wheel, and rotating housing. The pump wheel connects to the driving shaft (input shaft), while the turbine wheel links to the driven shaft (output shaft). These components face each other, forming a sealed working chamber filled with hydraulic fluid (typically oil).
Energy Conversion and Transmission
Pump Wheel Function: When the driving shaft rotates the pump wheel, the fluid within follows the blades' motion. Centrifugal force propels the fluid toward the pump wheel's outer edge, generating high-speed, high-pressure flow. This process converts mechanical energy into fluid kinetic energy.
Turbine Wheel Function: The high-speed fluid flows from the pump wheel into the turbine wheel. Due to the rotational speed difference between the two wheels, the fluid impacts the turbine blades, driving the turbine and outputting mechanical energy via the driven shaft. This step completes the conversion from fluid kinetic energy back to mechanical energy.
Fluid Circulation and Coupling
The working fluid circulates continuously between the pump and turbine wheels. It moves outward from the pump wheel's inner edge, enters the turbine wheel, decelerates, and returns to the pump wheel's inner edge, forming a closed-loop "torque circle." This cyclical flow couples the pump and turbine wheels, enabling energy transfer.
Speed and Torque Regulation
A fluid coupling adjusts speed and torque within a specific range. When the load changes, the turbine wheel's speed varies, altering the speed difference between the pump and turbine wheels. This change modifies the fluid circulation rate and impact force on the turbine, thereby adjusting output torque and speed to match load demands.
Speed Control Function
The driven shaft's stepless speed regulation is achieved by adjusting the fluid volume inside the working chamber. For example, a scoop tube adjustment mechanism can alter the oil level to control transmitted torque and rotational speed.
Summary
The fluid coupling transmits and regulates mechanical energy through fluid kinetic energy transfer and circulation. With its simple structure and reliable performance, it is widely used in industries such as power generation, metallurgy, and petrochemicals, particularly in variable-load equipment like water pumps and fans.